Contact Us

PVC Wood Plastic Foam Door Panel Production Line
- Commodity name: PVC Wood Plastic Foam Door Panel Production Line
- Product Description
-
Using specially designed screw machine barrels, molds, and extruder processing production processes to produce wood plastic products. Company product series: Wood plastic one-step thick board equipment; Wood plastic one-step profiled equipment; Wood plastic one-step decorative material equipment; Wood plastic granulation equipment; Various wood plastic molds. The extruder can be used for single machine two-stage mixing and direct extrusion, or for two-step extrusion after granulation, which saves power and space. It has high output and stable extrusion pressure. The preheating feeder is placed on the top of the main machine, first extracting most of the residual water in the wood powder, making the main machine feeding section more substantial; The characteristics of good plasticization mixing effect. The optimized screw design reduces cutting and makes it difficult to cut wood fibers, resulting in a uniform residence time of the material inside the machine. The screw barrel is treated with bimetallic material, which is wear-resistant and corrosion-resistant, greatly extending its service life. This production line can produce PE, PP, or PVC wood plastic profiles, mainly used for pallets, packaging box boards, flooring, outdoor decorative materials, etc., with a wide range of uses. High levels of wood powder and plant fiber addition (up to 50-75%); The equipment has strong adaptability and can process PP, PE, ABS, PS, etc. simultaneously.
Production Process:
● Raw material preparation: Firstly, it is necessary to prepare raw materials such as PVC resin and wood powder, which will be mixed to manufacture wood plastic composite materials.
● Mixing and extrusion: Mix PVC resin and wood powder in a certain proportion, and add necessary additives such as foaming agents, stabilizers, etc. The mixed raw materials are fed into specially designed SJSZ80 or SJSZ92 conical twin screw extruders for extrusion.
● Foaming treatment: During the extrusion process, by precisely controlling temperature and pressure, the foaming agent in the raw material is activated to form a uniform microporous structure, thereby achieving foaming effect.
● Shaping and cooling: The extruded door panels are shaped through a vacuum shaping table to ensure the stability of product size and shape. Subsequently, the door panel is cooled through a cooling system to fix its shape and size.
● Cutting and post-treatment: The cooled door panel is cut according to the required size by a cutting machine, and then subjected to post-treatment processes such as polishing and painting to improve the aesthetics and durability of the product.
Features:
● High automation control: The PVC wood plastic foam door panel production line adopts PLC programmable computer control, with reliable and stable overall control, improving production efficiency and product quality.
● Energy saving and environmental protection: The foaming technology used in the production line can effectively reduce product weight, reduce material usage, and improve the insulation and sound insulation performance of the product, meeting the requirements of energy conservation and environmental protection.
● Superior product performance: The produced wood plastic foam door panel combines the advantages of wood and plastic, not only having the appearance of natural wood, but also overcoming the disadvantages of natural wood such as easy corrosion and deformation, and has better durability and stability.
● Easy and reliable operation: The production line is equipped with imported frequency converters and temperature control instruments, which have the characteristics of wide adjustment range and high temperature control accuracy, making operation convenient and reliable.
● Strong adaptability: The production line can adjust process parameters according to different product requirements, produce wood plastic foam door panels of different specifications and styles, and adapt to diverse market demands.
Main Technical Parameters Model YF180
YF240
YF300
YF600
YF900
YF1200
Maximum Board Width (mm) 180
240
300
600
900
1200
Traction Height (mm) 150
150
150
150
150
150
Traction Force (KN) 2
2
2
30
40
50
Traction Speed (m/s) 0-5
0-5
0-5
0-3
0-2.5
0-2.5
Total Power of Auxiliary Equipment (kW) 35
35
30
30
40
45
Auxiliary Cooling Water Capacity (m³/h) 6
6
6
9
12
15
Compressed Air Pressure (Mpa) 0.6
0.6
0.6
0.6
0.6
0.6
Keywords:
Shipping Photos
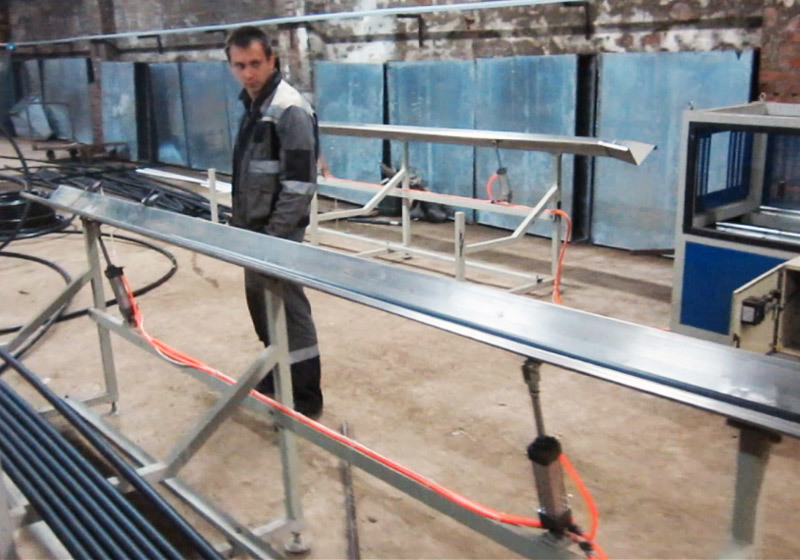
Export to Russia
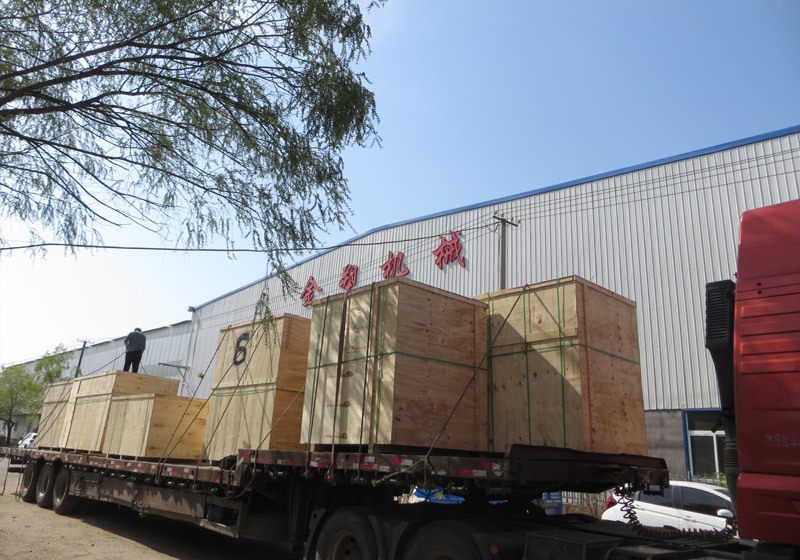
Export to Rwanda
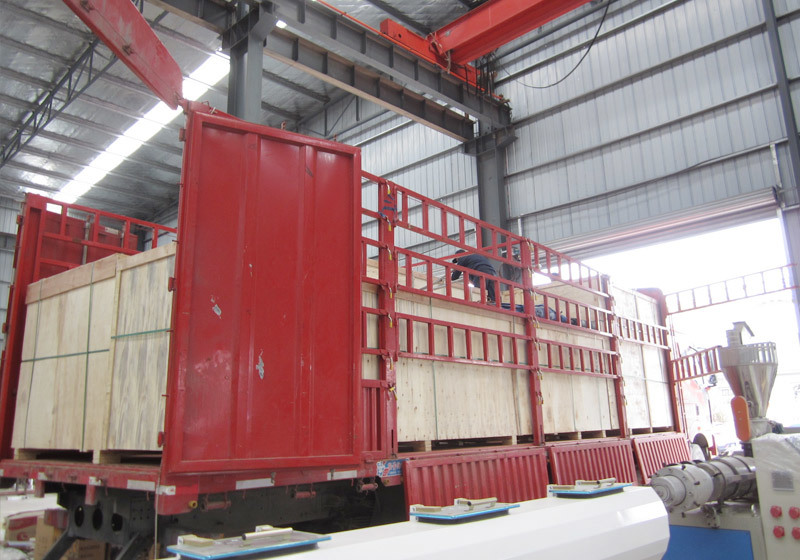
Export to Cameroon
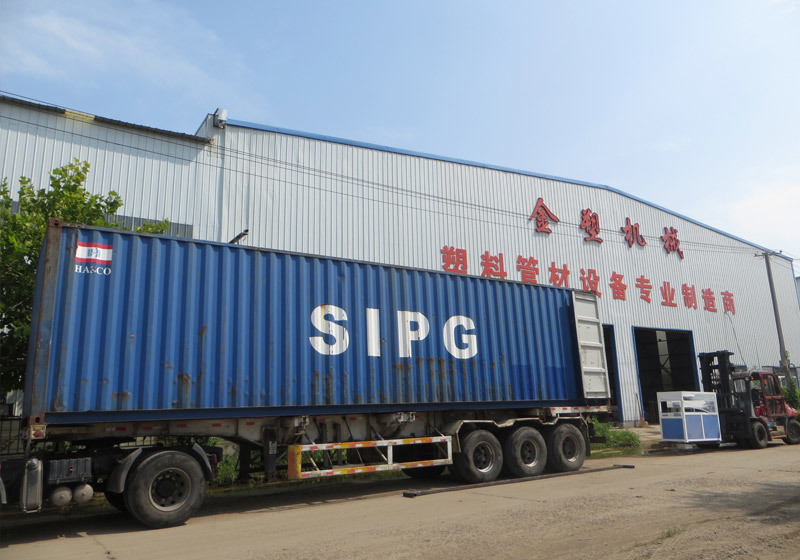
Export to Vietnam
Factory Workshop
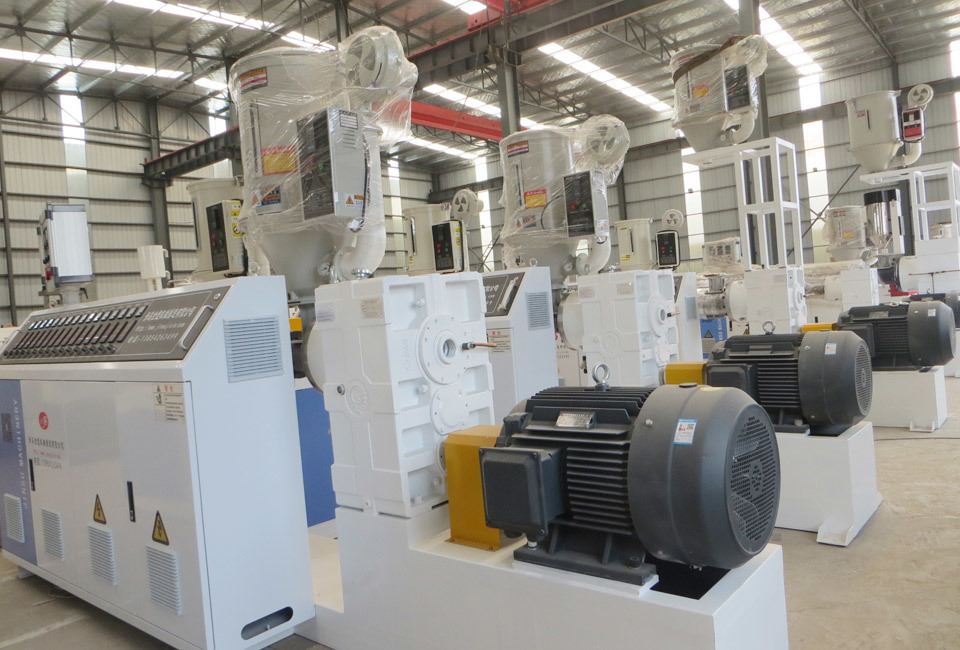
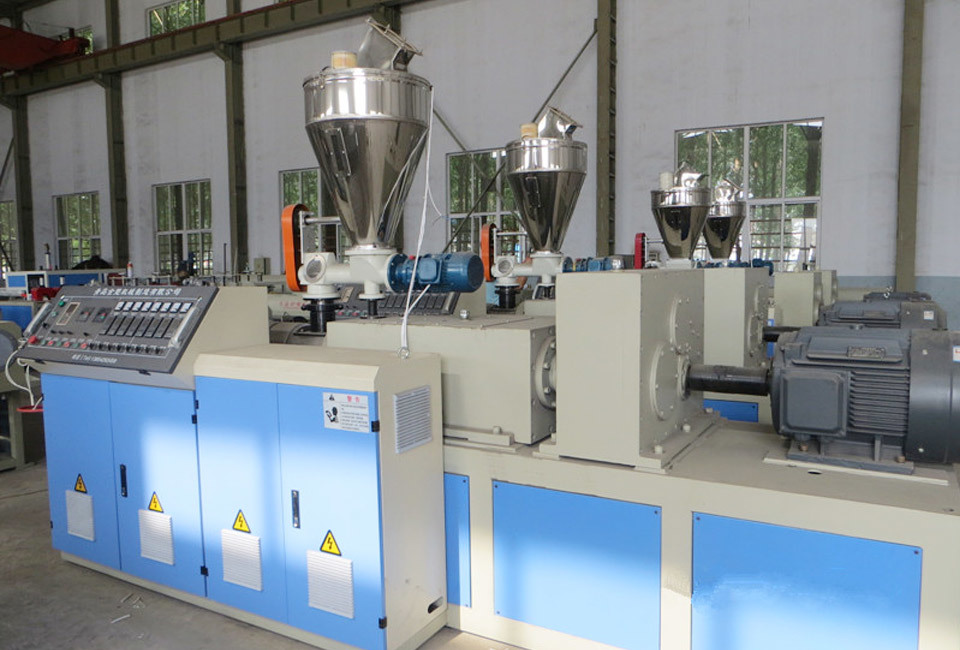
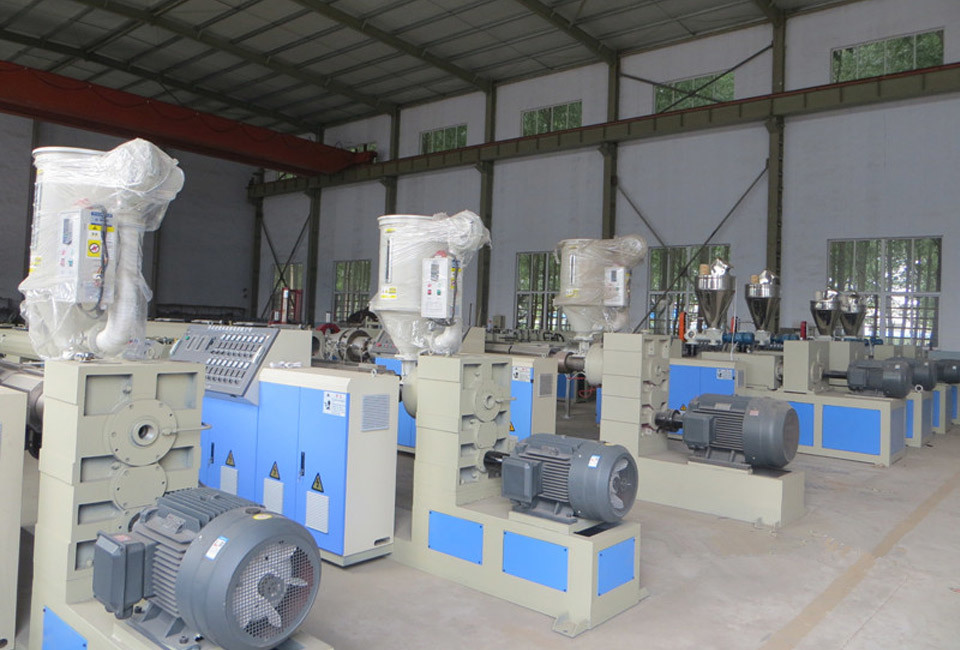
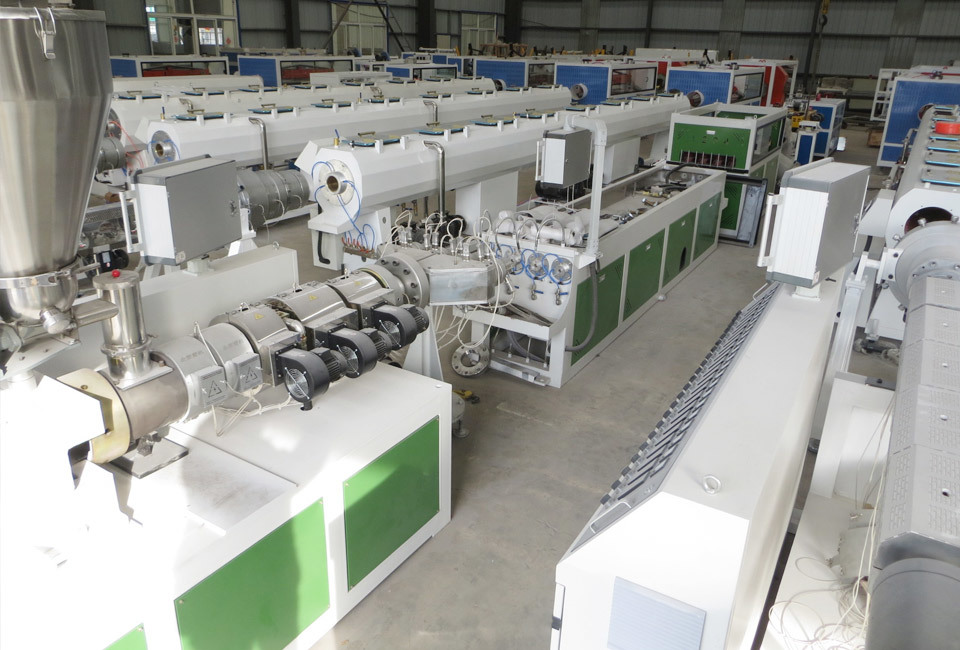
FAQ
01
Are we manufacture or trade company?
02
What kind machines we produce?
03
What kind payment we accept?
04
How long we need to produce the machines?
05
Will the machine be delivered on time ?
06
How about the machine quality?
07
How about the price?
08
How long is your machine’s guarantee time?
09
What can you provide for after sale service?